My journey with 3D printing since 2017
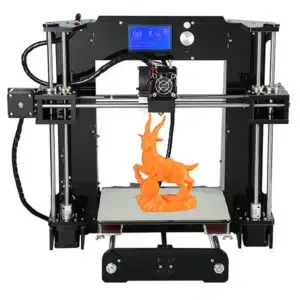
Back in 2017, I bought my first 3D printer—an Anet A3 from AliExpress—which I still have to this day. I can vividly remember the excitement and nervousness I felt from the moment I placed the order online to the day it arrived in Mexico, two weeks later. The anticipation was killing me. The moment I received it, I wasted no time and immediately started assembling it. At that time, I was in the final year of my engineering degree in physics, studying as a foreign student.
That weekend, my parents came to visit me and my brother, but I was so obsessed with the printer that I spent 12 straight hours assembling it, completely inmersed in the process until I finally finished at around 4 AM.
I can still remember the distinct smell of PLA filament burning in the nozzle for the first time—using that cheap test filament that came with the printer. Decided to put my printer to good use, I decided to print a capo for my guitar—because, of course, I had tons of hobbies. The result? It turned out... good-ish! At that moment, I felt invincible—like the entire world of engineering was at my feet. The possibilities seemed endless! Should I start a company? Should I develop and commercialize a product?

Despite my lack of experience in product design and sales, I knew that everything I needed to succeed was on YouTube. That didn’t stop me from taking the plunge and starting my first "company." By that, I mean creating a Facebook and Instagram account, along with a customized Gmail address. And just like that, 3D Option was born.
I was so committed to making something positive out of my first 3D printer, especially since I had bought it with an award I received from a research contest. I had presented our work on superconductive materials—a project proposed and strongly supported by my research supervisor. I was beyond excited to participate, and to my surprise, we won 1st place!
The reality? My “company” wasn’t exactly a success. I posted my services on various marketplaces multiple times but had little to no traction during the first year. However, that printer proved to be incredibly useful for my final-year project. I spent countless hours learning SolidWorks to design an automatic pill dispenser. Every part of it was 3D printed, and thanks to the skills I gained from two electronics courses—both analog and digital—my team and I developed a very interesting "product" that received amazing feedback during our presentation.
To this day, I still don’t understand why we got a 95/100 instead of a perfect score, but I guess it wasn’t as magnificent as I remember. In the end, though, I can confidently say that my printer was used wisely! It helped my team and me to deliver a great project. Back then, 3D printers were not as common, and even in an engineering school, there were no printers available for students like us, so delivering this project was a big deal.
Years went by, and as I started receiving more orders for 3D Option, the limitations of my Anet A3 printer became more evident. It struggled printing more advanced materials, and its productivity was precisley helping as it was just too slow. After graduating, I started an internship, and with my first paycheck, I bought two Ender-3 printers from Creality, also from Aliexpress. My plan was to use one and sell the other—and it worked! I sold one and used the profit to buy two more, eventually working with three Ender-3s alongside my trusty Anet A3.
Ironically, in that moment I was a strong critic of Ender printers, thinking they were nothing more than toys. How could something be assembled in just 20 minutes and be ready to print? Where was the excitement of spending 12 hours assembling something that could potentially short-circuit your entire house? But, to my surprise, the Ender printers were amazing. They significantly increased my printing volume, and over time, I grew to love them.
3D Option started growing steadily. I found a customer who placed an order every three months—a large and consistent demand that allowed me to invest in a good stock of materials and improve my workshop setup, which, at the time, was just a room in my house. The orders kept coming in regularly, and I eventually reached a point where I could no longer manage the business on my own, as I had taken on a demanding full-time job. Realizing I needed help, I reached out to a former classmate, and we decided to split the profits 50/50. He handled the printing and post-processing, while I focused on designing, managing expenses and supplies, and seeking new customers. However, just as things were starting to take off, a huge opportunity came my way—one that made me put those plans on hold.
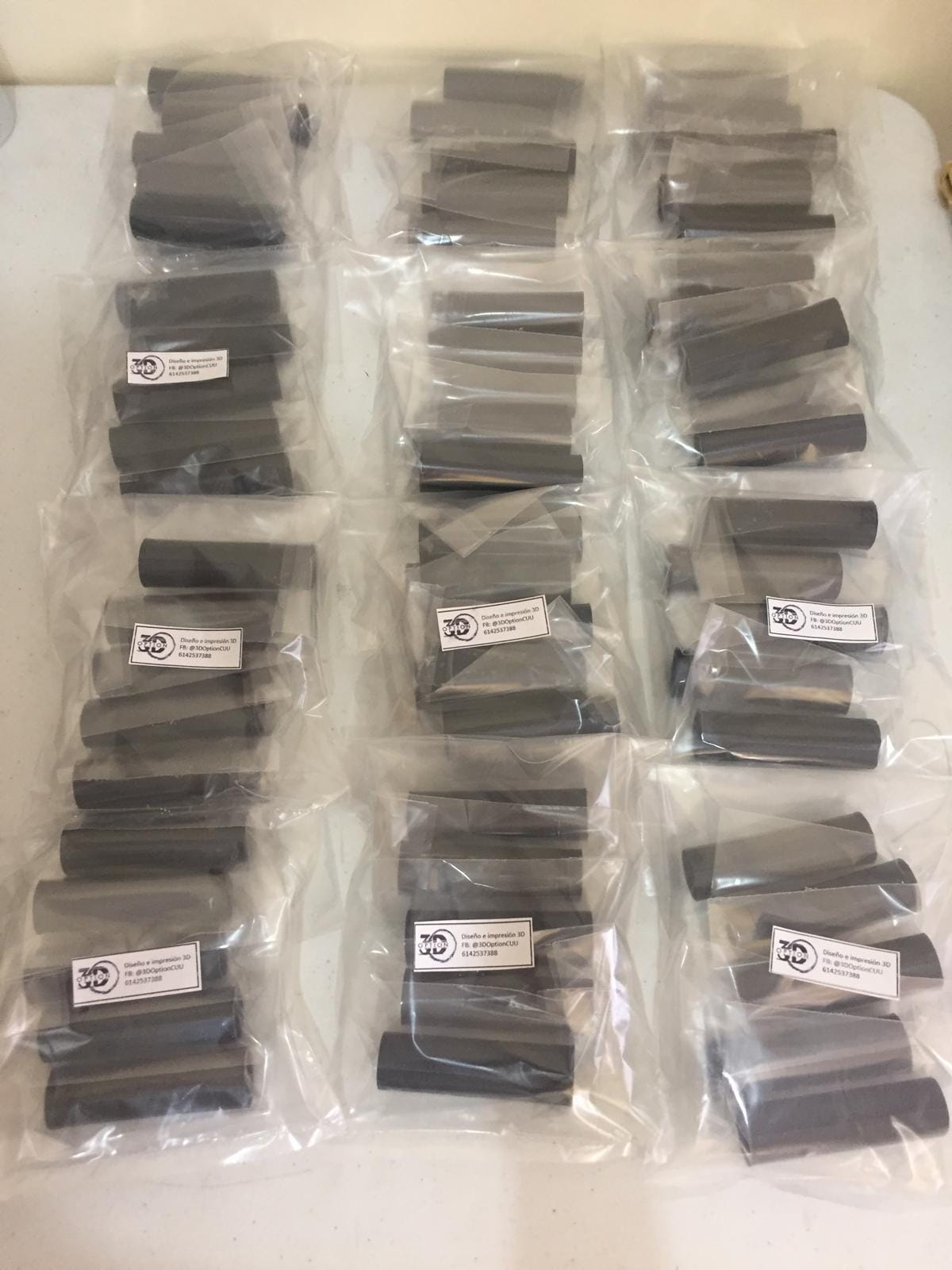
Today, I live in another country, pursuing a PhD in materials science, and obviously I’m no longer able to work with my printers. However, in my lab, we have an Ultimaker A5—an expensive £5,000 machine—but to be honest, I still find my cheap Ender-3s more reliable. Funny enough, when I told a colleague about my passion for 3D printing, he introduced me to a lecturer who was setting up a lab for his module... using Ender-3 printers! It felt like a sign from the universe and turned out to be a great experience.
3D Printing in My PhD Research
In my PhD research, 3D printing and design have been incredibly valuable tools. My work focuses on developing free-standing electrodes for supercapacitors, which are fabricated by carbonizing electrospun materials. As I progressed with my project, I realized that the available setups in my research group were not fully suited to my specific requirements. To address this, I designed a custom rotating drum collector made from solid aluminum, ensuring uniform thickness along its perimeter.
To complement the drum, I utilized 3D printing to fabricate the stand and electronics enclosure, incorporating threaded inserts for easy assembly. Additionally, I developed a motorized platform that moves back and forth to achieve uniform fiber distribution across the drum. This platform was also 3D printed, with the motion rail creatively repurposed from an existing setup. By integrating 3D printing into my research, I have been able to rapidly prototype, customize, and optimize components, ultimately enhancing the efficiency and precision of my experiments.
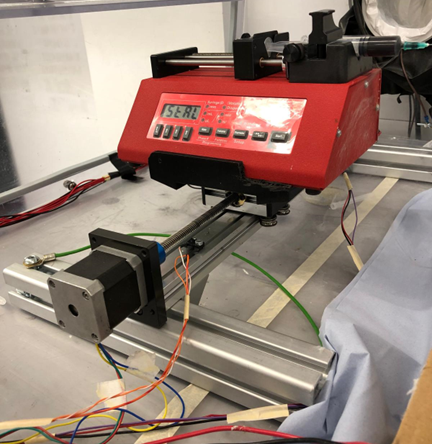
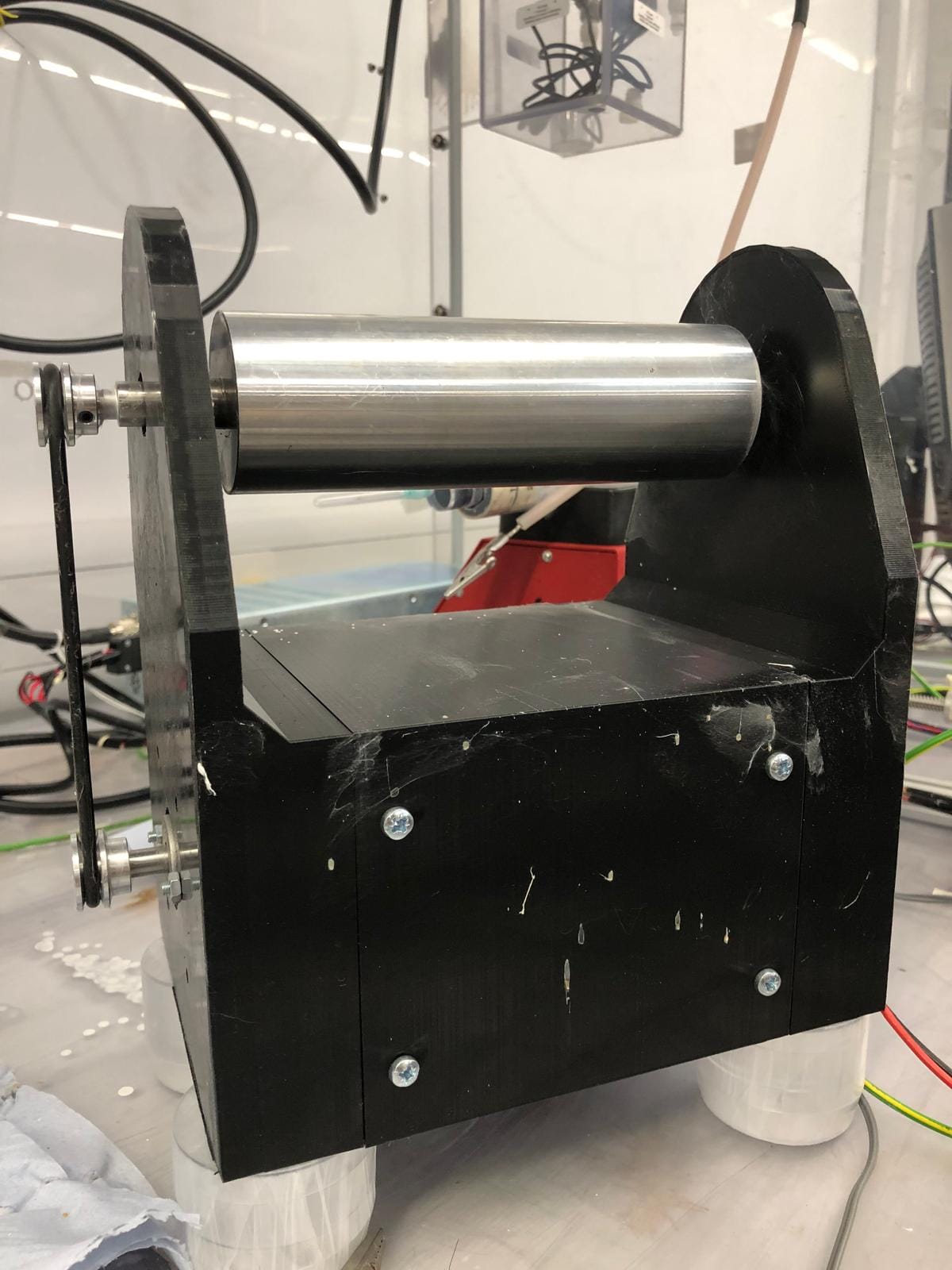
As part of my research on electrodes, testing the electrochemical performance of my materials is crucial. To facilitate this, I designed a custom Swagelok-type cell, allowing me to evaluate my supercapacitors across a wider range of electrolytes. The cell was 3D printed using resin, providing high precision and chemical resistance, and features glassy carbon electrodes as current collectors. To ensure a secure and leak-free assembly, I incorporated 6 mm O-rings, effectively preventing any electrolyte leakage and minimizing potential artifacts in electrochemical measurements.
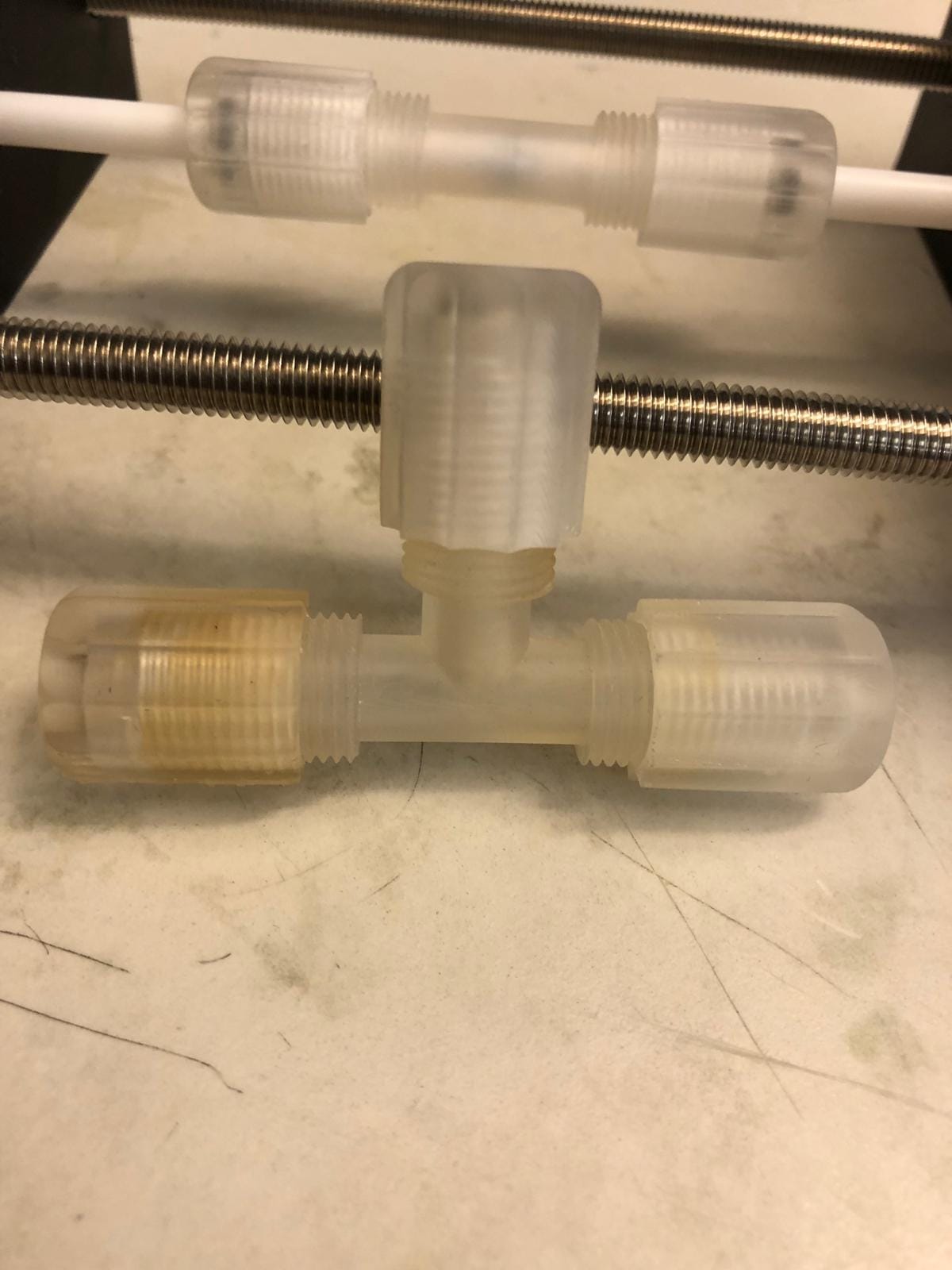
This customized cell has enabled me to conduct more reliable and reproducible electrochemical tests, contributing to a deeper understanding of my materials' performance under various conditions.
My last 3D printer so far
This past Christmas, I my wife gave me a BambuLab A1 Mini, and it’s incredible how far 3D printing technology has come. This new printer is a beast. You can start printing within 10 minutes of unboxing, control everything from your phone, and the speed is three times faster than my previous printers, with unmatched quality.
After setting up five of my own printers and helping set up over seven in different labs, I must say—every time I start a first print, it takes me back to 2017. Back to when this journey began—one that has opened so many opportunities and has been with me every step of the way.