Would it be possible to 3D print a 3D printer?
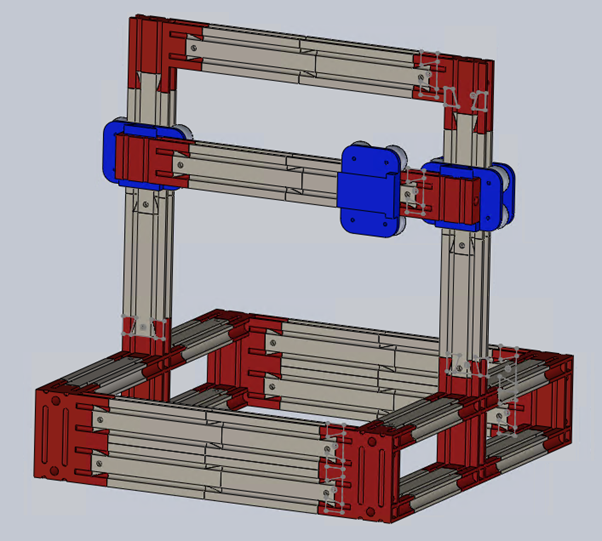
I'm pretty sure I'm not the first person to wonder about the possibility of printing a 3D printer with a 3D printer. Is that 3D printer...ception? Okay, bad joke.
The exciting part of this project, however, is that I plan to make it modular. In other words, each section will be designed to be easily replaced or expanded as needed.
Why?
Typically, makers are limited by the dimensions of their devices—whether it's 3D printers, laser cutters, or CNC machines. It's understandable; for instance, if the rails are driven by long screws—often (and incorrectly) called "infinite screws"—there's a physical limit to how long they can be. The same applies to the X and Y axes of a 3D printer. Even if they're driven by tension belts, those belts have a fixed length.
Addressing these limitations is one thing, but there's an even greater challenge: the frame. It's not as easy to modify. With a modular approach, the frame can be expanded as much as needed.
Consider this: why is a 300 x 300 x 300 mm 3D printer often several times more expensive than a 200 x 200 x 200 mm model? Simply put, it's because demand varies. It's far more common for an early DnD enthusiast to get a 3D printer to print their party’s characters than for someone to print a replacement car part. But what if that changed? Would they need to buy an entirely new, more expensive machine?
Not necessarily. Many components, such as motors, rails, motion systems, extruders, cooling systems, and even software, could remain the same. The idea here is to make scalability accessible and cost-effective.
How?
You might be thinking, "But that's impossible!" And you might be right—if the entire printer were 100% 3D printed. However, the plan is to incorporate a well-known engineering and materials science concept: composites.
Composites typically combine two materials with complementary properties. For example, airplane seats are made of resin and a honeycomb structure. The resin provides rigidity and holds everything together, while the honeycomb shape ensures lightweight strength and pressure resistance. It's somewhat similar to tensegrity, where one component provides tension, another provides compression, and together they create structural equilibrium. (I hope my analogy holds up!)
In this case, the printer’s body will be primarily made of 3D printed parts, but its structural integrity will come from an internal "soul"—much like the truss rod in a guitar neck, which reinforces and stabilizes the instrument. Instead of a metallic rod, the plan is to use a carbon fiber tube, offering strength without adding excessive weight.
Moreover, the entire design is tailored to be printable on small 3D printers—specifically because I own a BambuLab A1 Mini.
I'll keep you posted...